For brushed DC motors, brushes are as important as a heart. They provide a steady current for the motor's rotation by constantly making contact and breaking apart. This process is like our heartbeat, continuously delivering oxygen and nutrients to the body, sustaining life.
Imagine your bicycle generator; as you pedal, the generator starts to work, and the brushes ensure the continuity of the current, illuminating your bicycle headlight as you move forward. This is a practical application of brushes in everyday life, quietly supporting our daily activities.
In the brushed DC motor, the role of the brushes is primarily to conduct electricity and to commutation. As the motor operates, the brushes contact the commutator, transferring current through friction and changing the direction of the current during rotation, ensuring the motor can continue to run. This process is like using a brush to brush across a surface, hence the name "brush."
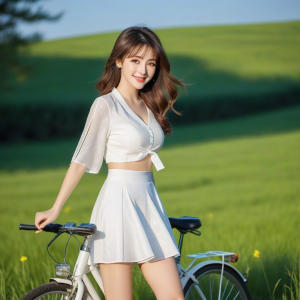

In layman's terms, the brush is like the "charger" of the motor; it continuously charges the motor's coils, allowing the current to flow in the right direction, thus enabling the motor to rotate. Just like in our daily lives with a remote-controlled car, when you press the button on the remote, the brushes are working inside the motor, allowing the car to run quickly.
Current Direction Reversal: In brushed DC motors, brushes are responsible for reversing the direction of the current as the motor rotates. This is achieved through the conductive contact between the brushes and the motor rotor. This process of reversing the current direction is essential for the continuous rotation of the motor.
Maintenance of Brush-Rotor Contact: The contact between the brushes and the motor rotor must be maintained to ensure the smooth flow of current. In high-performance motors, this requires brushes with excellent wear resistance and conductivity to reduce friction and resistance.
Motor Performance Adjustment: The performance of the motor can be adjusted by changing the material and design of the brushes. For instance, using high-performance brush materials can enhance the motor's efficiency and power density.
Management of Brush Wear: Due to the friction between the brushes and the rotor, brushes will wear over time. In the design of high-performance motors, effective strategies are needed to manage brush wear and ensure the reliability and lifespan of the motor.
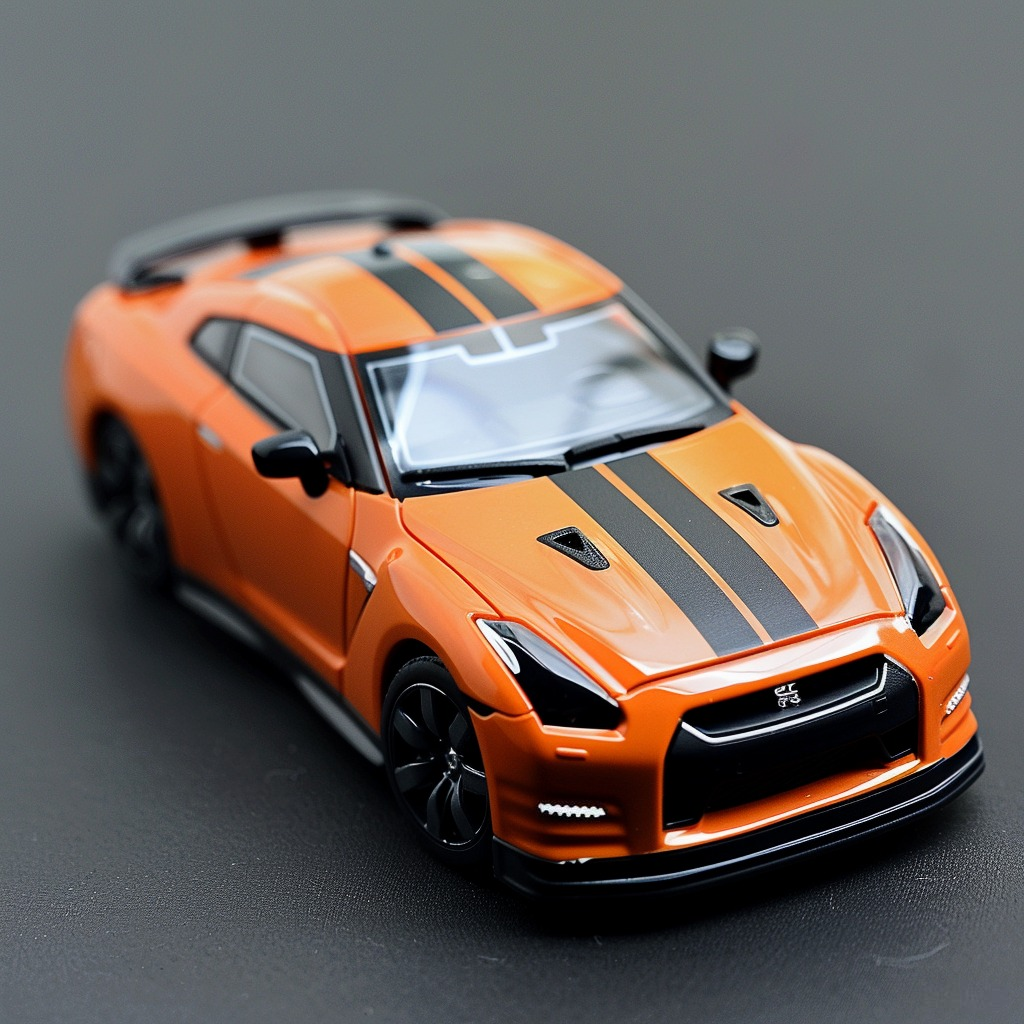
Sinbad Motor is committed to developing high-performance motor equipment solutions, known for their exceptional performance, efficiency, and reliability. Our DC motors utilize NdFeB high-torque materials and have been widely applied across various industries, including medical, automotive, aerospace, and precision equipment. We offer a complete range of micro drive system integration solutions, encompassing precision brushed motors, brushed DC motors, and micro gear motors.
Editor : Carina
Post time: Apr-13-2024